Logistics Company Optimization
A local logistics and warehouse company with over 20 employees and 25,000 SQ Ft of facilities solicited our help to drive down their costs
Within one month, we standardized and streamlined their processes, saving them over $50,000 in labor hours per year.
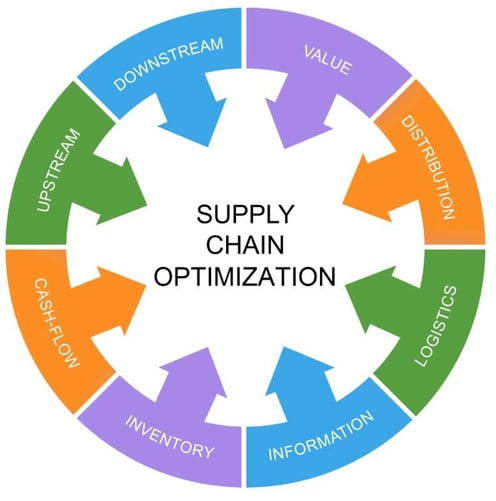
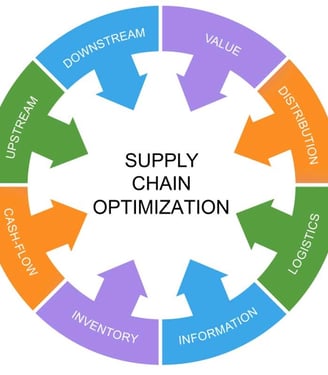
The company had gone through a series of acquisitions and did not have defined roles and responsibilities. Processes were not standardized and the lack of SOPs did not help the organization during this transitional period.
BBG conducted an in-depth analysis of all employee operations. During our analysis, we identified major inefficiencies and non-value add activities in their purchase and fulfillment process that were hurting the organization's profitability.
We streamlined all of the processes, created new SOPs, and distributed them amongst all of the employees to clear up any ambiguity. The new process was so efficient it eliminated the entire role of an employee and allowed the organization to transition him elsewhere without jeopardizing their operation.
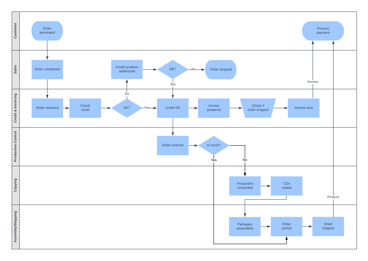
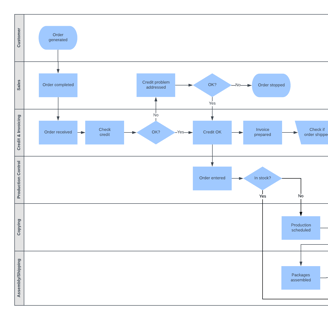